一、引言
在工业领域不断革新的当下,工业 4.0 概念引发全球制造业变革。电加热硫化罐作为橡胶等行业的关键设备,其智能化改造与工业 4.0 的结合成为提升生产效率、产品质量以及企业竞争力的重要路径。
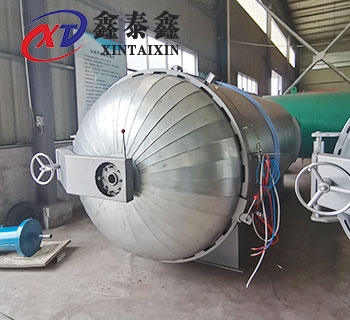
二、电加热硫化罐智能化改造的必要性
传统电加热硫化罐的弊端:传统电加热硫化罐依赖人工操作,硫化过程中温度、压力控制精度欠佳,导致产品质量稳定性差。例如在橡胶制品硫化时,温度波动可能使橡胶硬度、弹性等物理性能出现偏差。人工巡检记录数据,不仅耗费人力,而且数据记录存在滞后性和误差,难以实时反映电加热硫化罐运行状态。
智能化改造的迫切性:市场对橡胶等硫化产品质量和生产效率要求不断提高,传统电加热硫化罐已无法满足需求。通过智能化改造,可实现硫化过程自动化、精准化控制,契合现代工业生产模式,提升企业在市场中的适应能力和竞争力。
三、电加热硫化罐智能化改造与工业 4.0 的结合点设备互联互通:运用工业以太网、物联网等技术,将电加热硫化罐与工厂内其他设备(如原材料输送设备、成品检测设备等)连接成网。每个电加热硫化罐配备传感器和智能终端,实时采集温度、压力、运行时间等数据,并上传至工厂数据中心,实现设备之间数据共享与协同工作。例如,硫化完成后,系统自动将产品信息传输至检测设备,启动检测流程。
自动化控制与优化:引入先进的自动化控制系统,替代人工手动调节硫化参数。根据不同产品硫化工艺要求,在系统中预设参数,系统依据实时监测数据自动调整温度、压力等,确保硫化过程精准无误。利用大数据分析和机器学习算法,对历史生产数据进行挖掘,优化硫化工艺参数,提升产品质量和生产效率。例如,通过分析不同批次产品质量数据和对应硫化参数,找出最佳参数组合,用于后续生产。
生产过程可视化:借助工业软件和监控平台,构建电加热硫化罐生产过程可视化界面。操作人员可在监控中心实时查看每个电加热硫化罐运行状态、参数变化曲线等信息,对生产过程一目了然。当出现异常情况(如温度过高、压力过低)时,系统自动报警并显示故障位置和原因,方便操作人员及时处理,保障生产安全稳定运行。
智能维护与预测性保养:在电加热硫化罐关键部件安装振动、温度、磨损等传感器,实时监测设备运行状态。通过数据分析预测设备故障发生概率,提前安排维护保养,避免设备突发故障导致生产中断。例如,当监测到某部件磨损接近阈值时,系统发出预警,提醒维修人员及时更换部件,降低设备维护成本和生产损失。
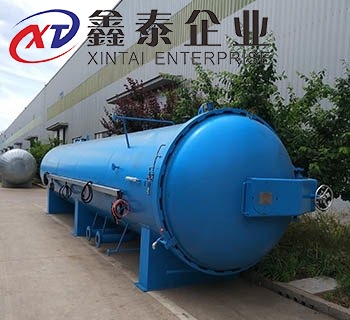
四、电加热硫化罐智能化改造的实施步骤
需求分析与方案设计:深入了解企业生产现状、产品工艺要求以及未来发展规划,对电加热硫化罐智能化改造需求进行全面梳理。根据需求制定详细改造方案,包括选用的智能化技术、设备选型、系统架构设计以及实施计划等。
设备升级与系统集成:按照方案对电加热硫化罐进行硬件升级,安装传感器、智能控制器、通信模块等设备。同时,将这些设备与工厂原有自动化系统、信息化管理系统进行集成,确保数据传输顺畅和系统协同工作。
软件开发与调试:开发电加热硫化罐智能化控制系统软件,实现参数设定、自动化控制、数据采集与分析、可视化监控等功能。在软件调试过程中,模拟各种生产场景,对系统稳定性、准确性和可靠性进行测试优化,确保软件满足生产需求。
人员培训与上线运行:对企业操作人员、技术人员进行智能化系统操作和维护培训,使其熟悉新系统功能和操作流程,掌握常见故障处理方法。在培训完成后,将智能化改造后的电加热硫化罐正式投入生产运行,并持续跟踪运行情况,及时解决出现的问题。
五、电加热硫化罐智能化改造与工业 4.0 结合的效益提高生产效率:自动化控制减少人工干预,缩短硫化周期,提升单位时间内产品产量。例如,原本一批橡胶制品硫化需要 8 小时,智能化改造后可缩短至 6 小时,生产效率大幅提高。
提升产品质量:精准的温度、压力控制确保硫化过程一致性,产品质量稳定性显著提升,次品率降低。如橡胶产品次品率从原来的 5% 降低至 1%,提高了产品市场竞争力。
降低生产成本:智能维护减少设备故障停机时间和维修成本;自动化操作减少人工需求,降低人力成本。例如,每年设备维修成本降低 30%,人力成本降低 20%。
增强企业竞争力:智能化改造使企业生产模式更加先进高效,能够快速响应市场变化,开发新产品,拓展市场份额,在激烈的市场竞争中占据优势地位。
六、结论
电加热硫化罐智能化改造与工业 4.0 的结合,是橡胶等行业实现转型升级的关键举措。通过设备互联互通、自动化控制、生产过程可视化以及智能维护等方面的改造,企业能够获得生产效率提升、产品质量优化、成本降低等多重效益,为企业可持续发展注入强大动力,在未来工业发展浪潮中赢得先机。